TAT METAL orders a full CMI technologies Continuous Hot-Dip Galvanizing Line (CGL)
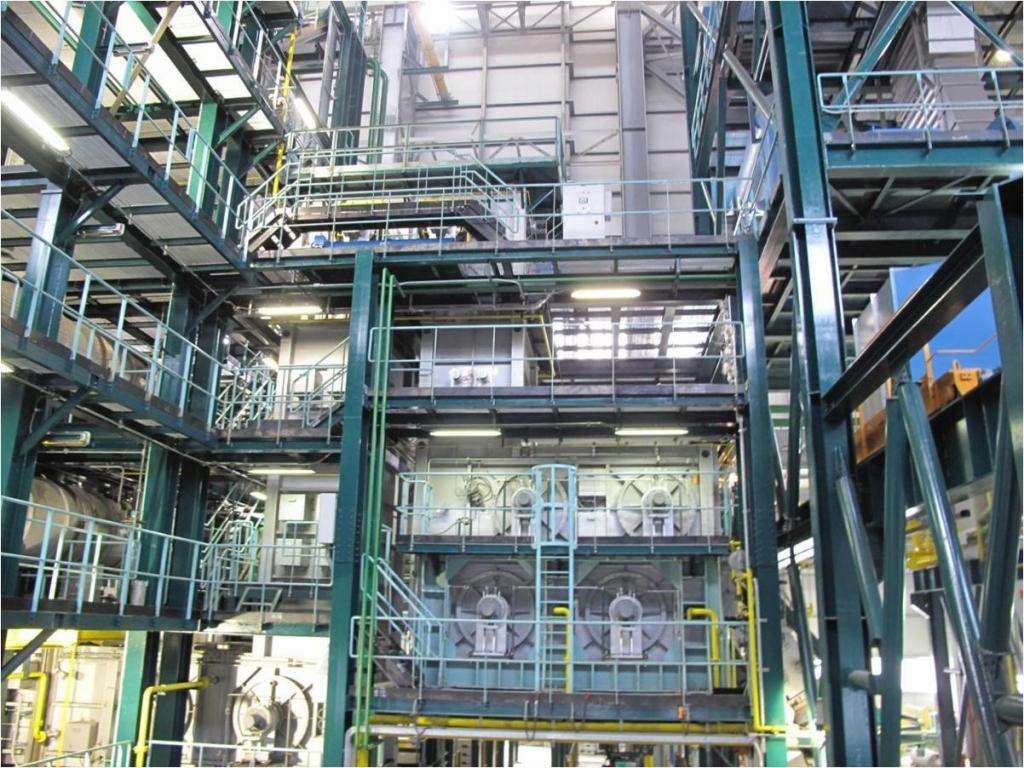
September 27th 2016
After having doubled their overall rolling, tempering and pickling capacity since 2011, Tat Metal, one of Turkey’s leading flat steel producers, has chosen CMI, with headquarters in Belgium, to supply their new, state-of-the-art hot-dip galvanizing line. The new line will allow the customer to increase its galvanizing capacity, in order to cater for a growing domestic steel market, but also to allow for increased exports to neighboring countries and Europe. The produced hot-dip galvanized steel is destined to be used to manufacture roll-formed shapes, steel structures for construction and components for automotive and “white goods”.
In order to support Tat Metal in its capacity expansion plans, CMI will supply a line, designed to galvanize 400,000 tons per year of steel strip, that will be installed in the customer’s steel works in Ere?li, Turkey. CMI will be in charge of the complete design of the line, the manufacture of some of the core machines, the supervision during erection and commissioning, as well as the coordination of all key subcontractors. Additionally the scope of supply includes some of the major components of the electrical and automation systems.
The line, aiming at a high level of operating efficiency and eco-friendliness, features all essential, high-quality core process technologies designed by CMI: Cleaning section, Vertical annealing furnace (incl. CMI’s L-Top math model and Blowstab® jet cooling system), Air-Knife system and Zinc bath equipment, APC Blowstab® low vibration cooling system, Inline skin pass mill and Tension leveler, Chemical roll-coat post treatment, Exit shear.
But it also incorporates a number of innovative features. As such CMI’s vertical annealing furnace provides recuperative low NOx burners, and the patented Blowstab® jet cooling system. Furthermore, CMI’s high-quality air-knife system will provide next to the patented Blowstab® low vibration cooling system, modern features such as a closed loop pressure system, an automatic lip cleaner and no-touch edge baffles. All of these features will allow the CMI air knife to achieve high-quality surfaces, while keeping zinc consumption low, and have convinced the customer to additionally order the upgrade of its existing Galvanizing line number 1 with the CMI air-knife system and zinc bath equipment.
The line will be designed for strips in thicknesses ranging between 0.25 and 3.00 millimeters and widths of up to 1,300 millimeters. The strip will be galvanized at a process speed of 200 m/min, while in the entry and exit sections speeds of up to 270 m/min will be attained.
The project is scheduled to be completed in a record-breaking time frame by the end of 2017.